About iRF Solutions
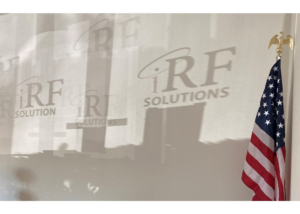

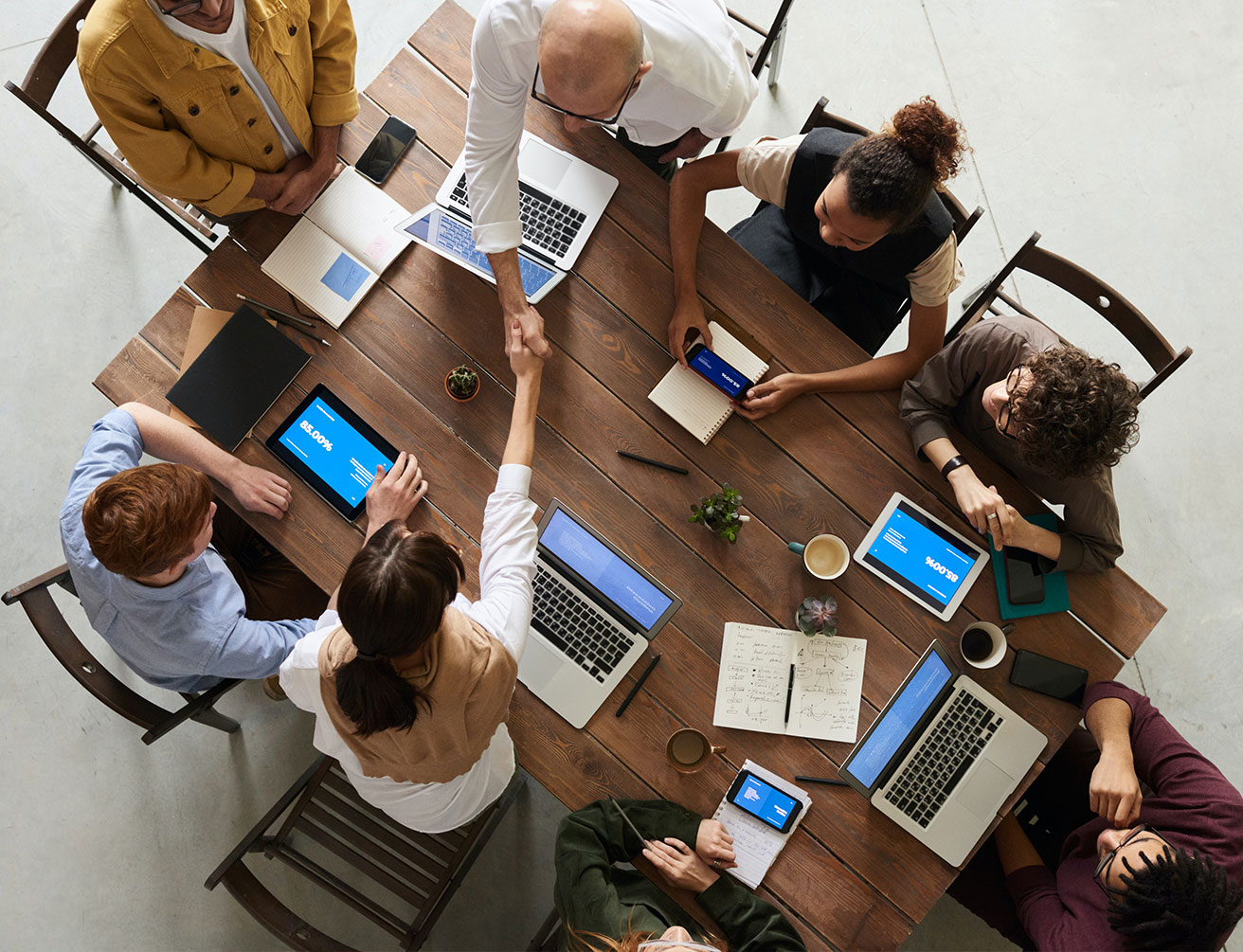
iRF and its predecessor, M/A-COM SIGINT Products, have over 50 years of experience providing high performance microwave RF solutions for the SIGINT and EW communities. Our products are deployed on a wide array of platforms (sub-surface, shipboard and airborne), rugged environments, and Specific Emitter Identification (SEI) applications. iRF core capabilities span the entire product development and production lifecycle, to include RF Engineering, Mechanical Engineering, Software Engineering, Integration & Test, Production and Product Support.
As part of iRF’s internal investments in research and development, we continue to align our product development efforts to support and drive modular and open architectures. Our product line engineering design methodology, supports opens system architectures such as SOSA, which standardizes interface data and control definitions between modules.
This approach supports future product development efforts through maximum re-use of technology, while reducing design cycle time and simplifying production logistics resulting in lower costs. This agile design approach permits ease of reconfiguration to address legacy and as well as future architectures, varying form factor requirements, RF microwave tuners, RF signal distribution and filtering, frequency Up/Down converters, and receivers.
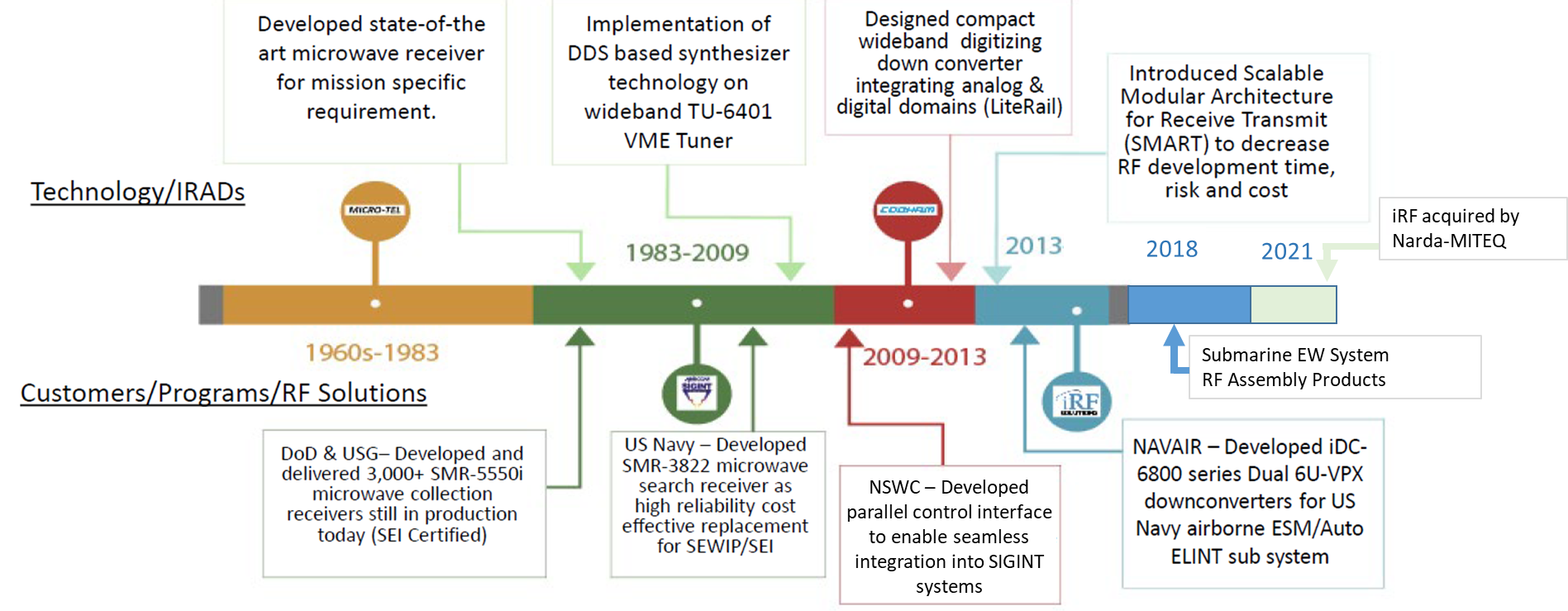
iRF Technical Capabilities
Minimized technical development risk critical to meeting our customers’ program schedule and performance requirements
- RF/Microwave System Design
- RF/Microwave multi-layer, mixed dielectric, SMT PCB-based circuit design
- VPX backplane and PCIe command/control
- High-speed digital design (FPGA and DSP)
- High-density mechanical packaging and interconnect
- Thermal management
- Production test and ATE development
- In-house filter design expertise
- Rapid prototyping capabilities
- Customer network emulation
- Full product lifecycle support
Proven Engineering Product Cycle – Design to Production
Product modifications and custom RF designs – Flexibility to adapt standard products or create new designs to support system specific requirements.
Concept development in tight collaboration with our customers
- Understand system and performance drivers & requirements
- Initial design concepts/approaches
- White paper development, Prototyping, Simulations and Measured Test Data
- Discuss design/performance/cost trade-offs
- Formulation of comprehension specification document(s)
Comprehensive proposal submission
- Management, technical and cost volumes
- FFP and T&M contract types support
New Product development
- Use proven RF design, mechanical packaging and software control reduces technical and schedule risk
- Typically 10 to 18 months for start from scratch design to beginning of production
- Product modification projects 3 to 12 months
- Support comprehensive First Article Qualification testing and environmental qualifications
Transition to Production
- Design engineers work closely with Automated Test group to develop needed fixturing and test/measurement software
- Design engineers currently provide high level of support to train production technicians on tuning/alignment and test
- Design improvements for manufacturing
Facility Manufacturing
- 25,000 sf engineering and production facilitated location in Sparks, MD
- Multiple Temperature Test Chambers used to characterize, calibrate and test all units over temperature extremes
- Dedicated ATE equipment racks with custom test with optimized software test suites to reduce test time and shorten delivery cycles
- In-house rapid prototyping and shock & vibration capabilities
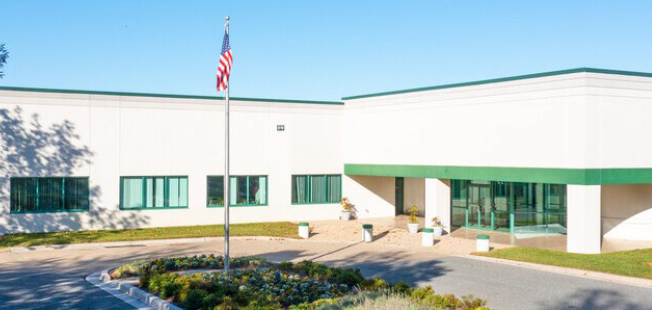